News
Lithium-ion batteries proved to be one of the most efficient energy storage solutions, widely used for applications such as electric vehicles [EVs] and renewables. Despite faltering economies and material shortages, more than 40 million EVs are expected on the EU’s roads by 2030. With mass electrification of transport, there will be an important demand for batteries and the materials they are made from. Despite an incentivising regulatory context at EU level, in 2023 Europe was home to only 1% of the production of key battery raw materials. European carmakers and battery cell producers are already fret about volatile prices and limited supplies of cathode and anode materials. But with EV fleet number growing on the EU’s roads, the volumes of End-of-life [EoL] batteries will considerably increase in the near future. And so will the pressure to recycle closer to home, recovering key components and mitigating the supply chain risks.
Conventional recycling methods often require high consumption of energy and reagents. But electrochemistry offers a promising green alternative method, enabling selective recovery of Li without the need for chemical extracting compounds.
Selective electrochemical extraction of lithium
Researchers at Chemistry Department of Sapienza University of Rome [UoS] tested various electrochemical parameters to optimise Li extraction from both commercial cathode material and the black masses [BM] obtained by the mechanical pre-treatment operations conducted in work package [WP] 4.
The electrochemical tests on high-purity commercial cathode materials [LiMn2O4, LiCoO2 and LiNi1/3Mn1/3Co1/3O2] allowed a selective extraction of Li up to 98 %. UoS researchers later applied the same electrochemical process on the black mass recovered by the mechanical pre-treatment, obtaining a lower Li extraction yield of 82 %. This decreased yield was mainly attributed to the presence of conductive carbon which undergoes a simultaneous electrochemical oxidation. Analysis of the resulting electrolyte at the end of delithiation experiments showed negligible extraction of cobalt (Co), nickel (Ni), and manganese (Mn). This demonstrated the method’s ability to selectively extract Li without causing the dissolution of other cathode elements.
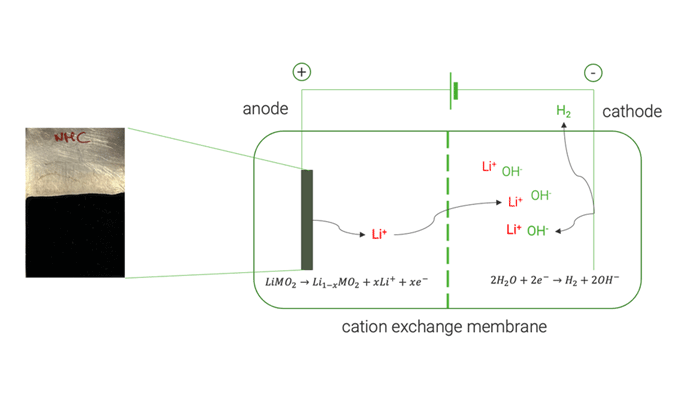
Cation exchange membrane | © Univ. of Sapienza
The optimised electrochemical conditions applied on the BM were replicated in a two-chamber cell to facilitate the separation and concentration of extracted Li on the cathode side, achieving approximately 85 %. The resulting solution was used to crystallise LiOH, resulting in a mixture of LiOH and LiOH·H₂O, with a purity exceeding 99.5 %.
Synthesis of reduced graphene oxide (rGO) and Li-Mn rich cathode material
The direct synthesis of high-value products from EoL LIBs, bypassing the complex and expensive separation of different metals, can be achieved through a competitive recycling strategy. The simultaneous synthesis of reduced graphene oxide (rGO) and lithium-manganese-rich (Li1.2Mn0.55Ni0.15Co0.1O2 – LMR) cathode material from EoL LIBs represents a promising approach to enhance the economic feasibility of hydrometallurgical recycling processes by producing high-value-added advanced materials.
UoS researchers developed an innovative recycling process to directly synthesise a layered LMR cathode and rGO from EoL LIBs. The proposed recycling strategy relies on the application of Hummers’ method to process the electrodic powder delivered by pilot-scale mechanical pre-treatment of mixed Li-ion batteries. The Hummers’ method has allowed for the quantitative extraction of metals from the electrodic powder and the production of GO without any metal impurity. The resulting solution contains the metals from the cathode materials (Co, Ni, Mn) with a significant amount of manganese from the KMnO4 used in the Hummers’ method. From such consideration stems the idea to synthesise LMR cathode material.
UoS researchers synthesised GO using the black masses obtained from three distinct EoL LIB pretreatments performed in WP4. The effects of thermal, mechanical and mechanochemical pretreatments were evaluated using the widely adopted Hummers’ method for graphene production. The study conducted by UoS researchers examined both pristine black masses and those subjected to metal removal via conventional acid leaching, a process frequently employed in LIB recycling to extract metals from cathode materials. This metal removal procedure had a notable effect on introducing oxygen functional group defects across all samples. A synergistic effect was particularly evident in the mechanochemically treated black mass, where acid leaching increased the GO yield significantly. This remarkably high graphite conversion to GO underscores the importance of selecting appropriate pretreatment methods for EoL LIBs, particularly when aiming to integrate advanced materials like GO into the recycling process.
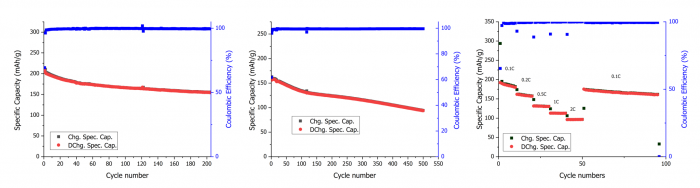
Cycling performance of LMR synthesised from thermally treated black mass: (a) Galvanostatic cycling at 0.1C, (b) Galvanostatic cycling at 1C, and (c) Rate capability performance with the current increasing from 0.1C to 2C every 10 cycles | © UoS
Recovery of Ni/Co materials by solvometallurgical route
RHINOCEROS is a research project that aims to o create economically and environmentally sustainable methods for reusing and recycling LIBs. The project focuses on developing cost-efficient, flexible and eco-friendly processes to recycle all materials in LIBs, including metals, graphite, fluorinated compounds and polymers.
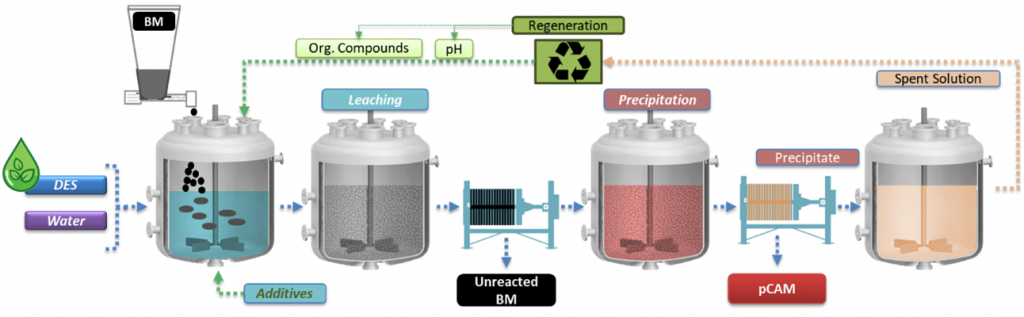
Flowsheet of the leaching, precipitation and regeneration process | © TEC
After studying the effects of the pre-treatment processes applied in WP4 to generate BM, researchers at TECNALIA [TEC] tested various solvometallurgical routes to extract critical metals like Ni, Mn and Co from LIBs under mild conditions. They established optimal process conditions to achieve leaching and precipitation efficiency along with high purity of the produced precursor of cathode active materials (pCAM) under mild conditions. This approach also enhances the recyclability of the extractant.
After characterising all the input materials received from the pretreatment operations, TEC research group analysed also the obtained leachates. The leaching process was optimised at laboratory scale by studying the effects of various parameters such as leaching time and temperature, stirring, waste/liquid ratio and additives.
The solvometallurgical process for recycling end-of-life [EoL] battery BM has successfully developed high-yield, selective systems, validated across various NMC chemistries and black mass pretreatments, achieving over 95 % leaching efficiency. Controlled precipitation delivered up to 95 % precipitation efficiency, producing precursors with more than 99 % purity, meeting project targets. Moreover, researchers have confirmed the scalability of the solvometallurgical process to large-lab testing without performance loss. To address the costs of this process, TEC researchers have also investigated alternatives to reuse and recycle the deep eutectic solvent [DES] leaching spent solution, reporting its dependence on the properties of the BM feed.
The residue after leaching – the graphitic anode material – has been purified via hydrometallurgical routes, underscoring the difficulty of removing the most refractory phases resistant to harsh leaching conditions.
Optimised recovery of materials from low concentration waste streams
A different task in the refining work package, led by LEITAT and TEC, aims at the recovery of low concentration materials from leachates and effluent streams produced in previous refining tasks. It is divided in three subtasks, each exploring different membrane-based technologies to achieve a zero-waste strategy for recovering remaining elements.
The objective of the first subtask is to develop new extractants based on ionic liquids or DESs, to be used within novel Polymer Inclusion Membranes (PIMs), for the recovery of Li from solvometallurgical refining final streams. The team firstly analysed the SoA on Li extraction strategies, selected, synthesised and characterised different potential extractants based on hydrophobic deep eutectic solvents (HDESs). Selected HDESs were synthesised and sent to the next subtask devoted to PIM fabrication and testing using different ILs and/or synthesized HDESs. These membranes represent an innovative technology that effectively adapts to the specificities of each input stream, enabling optimal recovery of valuable metals present in the waste generated by processes carried out. In the this subtask, the PIMs yielded the following recovery rates:
- Co and Mn: efficiencies close to 80 %
- Ni: 60 % recovery
- Li: only 19 %, but exhibiting a high flux rate of 1.2 mol/m²·h, suggesting potential for larger lithium recovery.
Finally, in the last subtask, researchers developed a three-chamber electrochemical process for the extraction, concentration and recovery of lithium in the form of lithium carbonate from solvometallurgical final streams. Different ion-exchange membranes were characterised and lithium carbonate precipitation step was studied and optimised. They tuned the overall process conditions achieving more than 70 % Li extraction from leachate to catholyte and high lithium carbonate precipitation yields (>70 %) with high purity (>94 %).
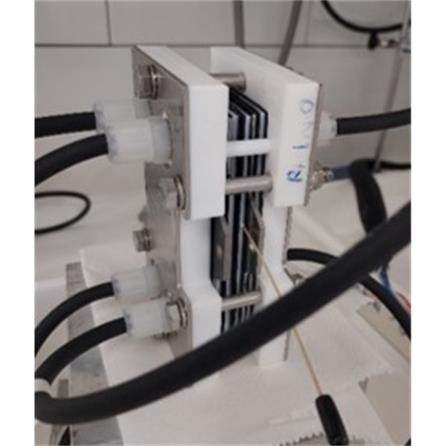
Three-chamber electrochemical cell | © TEC
Extraction of Ni/Co/Mn/Li with GDEx
Gas-diffusion electrocrystallisation [GDEx] is an innovative electrochemical process used to recover metals from complex fluids, such as leachates, industrial waste streams and organic solutions. This innovative process has been successfully demonstrated in multiple research projects, proving its capability to recover valuable metals while operating under low-cost and environmentally friendly operating conditions. The GDEx process has achieved Technology Readiness Level [TRL] 3 for the recovery of Co and Mn from synthetic solutions and attained TRL 4 in treating black mass leachates. One of the multiple advantages of this electrochemical process is its capacity to recover Ni, Co and Mn simultaneously, with the flexibility to manipulate operational conditions to obtain targeted products.
Specifically for the battery recycling sector, the GDEx process offers various advantages over conventional battery recycling methods:
- High recovery efficiencies, exceeding 90 % for Co and Mn and over 90 % for Li, with potential for further optimisation.
- Low energy consumption: less than 20 kWh per kg of recovered material, which reduces the operational costs significantly.
- Minimal chemical input: the process relies primarily on air and in-situ synthesised oxidising/reducing agents, ensuring high material efficiency and circular use of non-hazardous chemicals.
- Mild emissions, with the possibility to further treat any effluents using conventional wastewater treatment methods.
- Low temperature operation: from room-to-mild temperatures [18 – 70 °C].
- Direct synthesis of functional battery materials, such as Co/Ni/Mn spinels and birnessites, which can be used to manufacture new lithium-ion battery electrode materials and eventually LIBs. This feature eliminates the need for additional refining steps, streamlining the production of new batteries from recycled material.
Within the RHINOCEROS project framework, researchers at VITO have been finetuning the operational parameters of their proprietary GDEx process, additionally testing and validating the recovered materials through the synthesis of high-performance electrodes for next generations batteries, demonstrating therefore the circularity, cost, environmental and social benefits of the solutions developed.
After testing the direct recovery route of Co, Ni, Mn and Li on synthetic solutions with the main objective to finetune the GDEx operating settings, VITO researchers have been implementing the process to the BM samples provided by the pre-treatment operations [ACC and TES] and to the aqueous extractants processed by the hydrometallurgical route explored by UoS and the solvometallurgical route explored by TEC. Additionally, they also documented the testing operations using a 3D phase diagram material library, mapping the formation of different materials based on Co/Ni/Mn concentration ratios from synthetic solutions.
The GDEx process applied on the leachate solution obtained from the BM provided by ACC achieved high recovery rates: 90 % for Ni, 89 % for Mn and 96 % for Co.
On the other hand, GDEx process implemented on the leachate solutions provided by UoS [originally from the BM of TES] results in the metal extraction efficiencies of 98 % for Ni, 68 % for Mn, and 96 % for Co. Sequential GDEx experiments have potential to improve the recovery efficiency by removing the impurities first and then the recovering the targeted metals. GDEx treatment on TEC’s leachate solution required optimisation due to the presence of high content of Cu and Al impurities.
With better results obtained on the lithiated nickel manganese cobalt oxide (LNMCO) material synthesised from the leached black mass provided by ACC [thermal pre-treatment], VITO researchers validated its electrochemical activity as a cathode material for LIBs with coin-type half cells. The recycled cathode material maintained a stable charge-discharge profile up to 50 cycles, with an initial charge-specific capacity of 37 mAh g⁻¹ and a reversible capacity of 26 mAh g⁻¹. Later, a batch with large amount of BM will be treated by GDEx process to optimise the electrochemical performance of the recycled electrode material.
After removing the targeted transition metals Ni, Co and Mn from the leachate solutions of the BMs, researchers used the same solution to extract lithium, recovering >99 % Li from the leachate of ACC BM.
The low-temperature or near-ambient operation condition of GDEx process eliminates CO₂ emissions, ensuring a clean and cost-effective approach to recovery of NMC precursor. This aligns with RHINOCEROS project goals, promoting a circular and sustainable battery materials economy. These results highlight the sustainability and scalability of the GDEx process, providing a carbon-free alternative for battery material production, aligning with global efforts to decarbonize critical raw material supply chains.
© visual: VITO
On 12 December 2024, the third edition of the annual workshop of the Cluster Hub “Production of Raw Materials for Batteries from European Resources” took place in Brussels, being co-organised by EU-funded projects RHINOCEROS, CRM-geothermal and CICERO. This third edition, along with an increasing number membership, confirm the hub’s role as a dynamic ecosystem that continues to generate innovations in the European battery materials sector.
The hub’s annual workshop, held as a satellite event of the Raw Materials Week 2024, provided once again a platform for presenting the most promising results from participating projects. Two technical sessions covered the entire battery value chain, from raw materials mining to recycling, while the opening conveniently portrayed the policy, the regulatory and strategic frameworks that support and drive the EU R&I initiatives in the battery sector.
Policy perspectives and supporting mechanisms for the battery sector
Susana Xara, Project adviser on raw materials at European Health and Digital Executive Agency (HaDEA), established the discussions tone, navigating through the insights of the Critical Raw Materials Act [CRMA] and the Net Zero Industry Act [NZIA] and focusing on their contribution to securing a sustainable supply of critical raw materials for the European battery industry.
Wouter IJzermans, BEPA Executive Director, presented the long-term vision and potential revisions of their roadmap, emphasising the importance of policy frameworks and incentives in promoting battery innovation and deployment across Europe.
The presentation of Vasileios Rizos from the Centre for European Policy Studies (CEPS) identified various barriers and challenges emerging from the EU policy framework on batteries, based on inputs from 20 companies across the entire battery value chain, including partners from the BATRAW project, member of the Cluster Hub since 2022. The representative of CEPS concluded with a set of policy messages referring to early dialogue channels established between policy-makers and various stakeholders. Before the legal requirements entry into force, this information exchange on availability of secondary data sets could enable stakeholders to assess the data quality, select suitable sets of information and identify potential data gaps.
Publicly available resources submitted by CEPS:
- Barriers and policy challenges in developing circularity approaches in the EU battery sector: an assessment – CEPS
- Implementing the EU digital battery passport – CEPS
- Compliance with the EU’s carbon footprint requirements for electric vehicle batteries – CEPS
Orchestrating the launch and on-going work of the Cluster Hub, PNO Innovation Belgium [part of PNO Group – leader in innovation and funding consultancy], represented by Dr. Nader Akil, concluded the first session with an overview of all EU funding programmes supporting research, innovation and investment in raw materials production for batteries. Additional to the upcoming funding opportunities and guidance on selecting the appropriate funding opportunities based on the status of technology, Dr. Nader Akil introduced another initiative launched by PNO Group – DIAMONDS4IF. This project supports the preparation of Innovation Fund applications, enabling the transfer of H2020 research results into successful ventures and securing investment funding.
Download Funding Schemes presentation
The third session of presentations commenced with an outline of the main findings of the LIFE DRONE project, which concluded in June 2024. Presented by Lorenzo Toro, process engineer at Eco Recycling, the project demonstrated the feasibility of producing high-quality NMC oxide and graphite from recycled batteries. The innovative process confirmed significant environmental benefits, with a reduction of 59 % in terms of kg CO2 eq. Additionally, one plant is estimated to treat 500 tonnes of batteries/year. The technical-economic evaluation of this industrial plant, with a potential capacity of 500 tons/year, showed a return on investment (ROI) of 31.64 % and a payback time (PBT) of 3.16 years. The analysis indicated that attractive payback times could be obtained even with varying prices for NMC and graphite.
Download LIFE DRONE presentation
RHINOCEROS presenting results of the Electrochemical Li recovery strategy from LIBs black mass
The electrochemical Li recovery from Li-ion battery black mass, investigated in the RHINOCEROS project and presented by Prof. Pier Giorgio Schiavi from Univ. of Sapienza reported Li extraction yields from end-of-life (EoL) LIBs in the range of 82 %, and faradaic efficiency compared to commercial cathode materials (close to 100 %). Researchers have investigated potential causes that could explain the relatively low selectivity ranges of Li and other metals available in black mass. The simultaneous oxidation of impurities found in the black mass can be a justified explanation for the preliminary results obtained. Experimental results show that the extraction percentages for Co, Ni, and Mn remain in very low ranges. When contemplating upscaling scenarios, Prof. Schiavi mentioned the researchers are evaluating an alternative approach that enables the treatment of larger quantities of powder without replicating the manufacturing process of LIB electrodes.
Download RHINOCEROS presentation
The session featured also presentations of other initiatives addressing the batteries recycling topic: Benjamin P. Wilson, Senior Scientist, Hydrometallurgy and Corrosion at Aalto University on behalf of the RESPECT project, Miguel Aguilar, researcher at LEITAT Technological Centre for the BATRAW projects, and Joana Gouveia [Researcher at the Institute of Mechanical Engineering and Industrial Management (INEGI) and America Quinteros [Researcher at LUT Univ.] for the ReLiEF initiative.
Author: KIT
Following previous work performed in work package 5, researchers from KIT further investigated the lithium (Li) extraction from black mass (BM) supplied by partners ACCUREC (ACC) and TES.
The BM provided by ACC consists of graphite, as well as transition metals such as nickel (Ni), manganese (Mn), and cobalt (Co), along with their respective oxides and impurities like copper (Cu), iron (Fe) and few fluorinated compounds. Li is present in the form of lithium carbonate (Li2CO3), lithium fluoride (LiF) and lithium aluminium oxide (LiAlO2). However, breaking off lithium aluminium oxide to a soluble Li-salt and removing fluoride contamination proved to be challenging.
Previous work reported the simultaneous incorporation of fluoride ions and decomposition of LiAlO2 using an excess of calcium hydroxide (Ca(OH)2) at elevated temperatures. More recent developments of the processes show improvement, especially decreasing considerably the amount of of Ca(OH)2 , while achieving a Li extraction of 87 %. Instead of heating the suspension, it is possible to initiate the reaction by liquid-assisted grinding in a planetary mill. The results show LiAlO2 is decomposed. However, the fluoride content is not efficiently removed.
In the BM supplied by the partner TES, most Li is present as lithium transition metal oxides (LiTMO) and a small amount of LiF. To enable Li extraction, this BM was reduced by reactive milling in Task 4.4 – Reactive milling for the production of metallic black mass (MBM). The obtained MBM consists of graphite, the metallic composite, lithium oxide and the oxidised reducing agent, along with some impurities like Fe and fluorinated compounds.
After investigating aluminium (Al) and calcium (Ca) in the previous steps, researchers at KIT performed tests to assess Li extraction using a magnesium (Mg) system, which presents various advantages, namely: avoiding, on one hand, the formation of Li salts with bad solubility, and relying on the other hand on insolubility of Mg in the high pH aqueous solution.
After aqueous extraction, researchers obtained a mixture of Li2CO3 and LiF. In the upcoming months, this mixture will be purified to a battery-grade material.
The Critical Raw Materials Act (CRMA), proposed by the European Commission in March 2023, was adopted by the Council one year later, on 18 March 2024, marking the last step in the decision-making procedure.
Looking back in time, less than three years ago, the raw materials was a topic exclusively tackled by ‘connaisseurs’. Today, it has become a strategic file, and the speed of its adoption shows need for action to secure a sustainable supply of critical raw materials (CRMs).
Standing at the core of the Green Deal Industrial Plan, together with the Net Zero Industry Act and the Reform of the electricity market design, the CRMA is a flagship initiative with a threefold objective: to increase and diversify the EU’s CRMs supply, to strengthen circularity, including recycling, and to support research and innovation (R&I) on resource efficiency and the development of substitutes. The bloc further consolidated this timely adoption with a set of complementary regulations and diplomatic initiatives, outlining a clear position ready to reduce reliance on third countries through export restrictions and screening for foreign direct investment across various sectors [e.g. forging strategic agreements with Chile, Greenland, Ukraine, Canada, Rwanda, and more recently Norway].
Read the official press release
Echoing the official communication, Commission Vice-President Valdis Dombrovskis declared for Euractiv: “Trade flows of critical raw materials are highly concentrated,” adding, “While we will continue to rely on imports, we need to massively diversify.”
The official document sets a threshold of 65% of the EU’s annual consumption of any CRM deriving from any single country. The CRMA establishes also a list of 34 critical and no less than 17 strategic raw materials considered crucial for the twin green and digital transition, as well as for defence and space industries.
In addition to the updated list of CRMs, the act introduces three targets for annual consumption of raw materials:
- 10% for local extraction
- 40% EU domestic processing threshold
- 25% of supply emanating from recycled material
These changes modifying the recycling target reflect the increasing importance of paving a circular economy model that ensures a sustainable supply of raw materials.
© visual: European Commission
Authors: CHA and PNO
An important component of a Li-ion battery (LiB), the electrolyte has a crucial role in the cell performance. The nonaqueous electrolyte is a multicomponent system consisting of a conductive salt, mainly LiPF6 (Lithium hexafluorophosphate – inorganic component), organic carbonate solvents and additives.
Numerous research initiatives are dedicated to the design of the electrolyte composition, aiming to optimized performance, increased safety, lifetime and streamlined costs. However, once a LiB reaches its end-of-life (EoL) stages, the electrolyte receives less attention in the favour of the valuable metals that can be recycled from the cathode: Li, Co, Mn, Ni, Al, Cu. Moreover, due to its volatility, toxicity and high flammability, the electrolyte recycling is less studied. When ignored, the spent electrolyte reacts with water to form fluoride, leading to its uncontrolled decomposition and/or evaporation, and thus generating an imminent environmental risk. Due to its composition that includes organic solvents, the presence of residual electrolyte in the black mass is considered hazardous, and it is often a reason hampering the recycling process.
Researchers at Chalmers University (CHA) ) developed a sub- and supercritical carbon dioxide (sc-CO2) extraction process to selectively recover the electrolyte from spent LiBs. Sc-CO2 extraction technologies are already widely employed in the food, beverage, pharmaceutical, and cosmetic industry. In a nutshell, sc-CO2 forms when CO2 surpasses its critical point at 31°C and 73.8 bar pressure. In this so-called supercritical state, CO2 demonstrates optimal mass-transfer characteristics and can be fine-tuned to alter its physicochemical characteristics by adjusting pressure and/or temperature. However, CO2 proves ineffective as a solvent for high molecular weight polymers and highly polar ionic compounds. However, the addition of a co-solvent or a modifier can significantly improve the solubility properties of sc-CO2, making this alternative a suitable process to selectively extract LiPF6 after solvent removal.
Researchers at CHA investigated different process parameters (pressure, temperature, extraction times) to understand their impact on the extraction behavior of different electrolyte solvents such as ethylene carbonate. Their analysis included both qualitative and quantitative results indicating the composition and the purity. Simultaneously, the research also monitored the process exhaust stream for potential formation of LiPF6 decomposition products. The findings showed that that the non-polar electrolyte solvents like dimethyl carbonate, diethyl carbonate, and ethyl methyl carbonate were successfully extracted using low-density CO2. The more polar electrolyte components such as ethylene carbonate and propylene carbonate were stepwise extracted by gradually increasing the system’s pressure. The developed technology is a game changer not only for electrolyte recycling but also for increased workplace and transportation safety due to removal of the flammable and hazardous substances from battery black mass. The simplicity of the processing design is an additional advantage of the technology.
© Photo credit: Adobe
During the past years, the increase in the use of lithium-ion batteries (LIBs) has become more prominent. An unsurprising trend, whatsoever, due to the widespread and rapid adoption of clean mobility applications, electronic devices, and energy storage systems. Despite their undeniable environmental and social benefits, several challenges lie ahead. In 2022, global lithium demand exceeded the supply despite an 180% increase, IEA reports. Recent communications already forecast the demand of lithium (Li) is expected to soar over the next decade, with mobility accounting for the main consuming market.
The current supply of primary resources is deemed insufficient for the growing demand. Approximately 60% of today’s lithium is mined for battery-related applications, a figure that could reach 95 percent by 2030, McKinsey reports estimate. But this rapid increase in the use of LIBs in EVs will introduce a large quantity of spent batteries in the near future. The alternatives to manage spent batteries include remanufacturing, repurposing and recycling, with the latter one playing a significant role from both ecologic and economic points of view.
Current recycling processes lack selectivity in recovery control and require significant consumption of reagents and energy. The research conducted by the RHINOCEROS partners at Sapienza University of Rome (UoS), Department of Chemistry, aims to develop an electrochemical process for selective extraction of Li from electrodic powder of end-of-life (EoL) LIBs. This concept simulates the charging process of a LIB with an aqueous electrolyte and a cathode material (counter electrode) that facilitates water reduction. The hydroxyls freed by water reduction and the Li + cations deintercalated by the anode will form a LiOH solution.
Using two samples – a commercial powder, respectively one coming from EoL LIBs, and testing the delithiation process using various parametres, UoS researchers obtained:
- Li extraction of 99% from commercial powder
- Li extraction of 82% from waste powder
The lower Li extraction on EoL electrode powders compared to commercial ones is due to the presence of SuperP [a high purity and structured carbon black powder with a moderate surface area for the lithium-ion industry], which oxidises under delithiation conditions.
Discover the scientific publication
Between 14 and 18 November 2022, the European Commission organised the 7th edition of the Raw Materials Week, gathering a wide range of stakeholders discussing policies but also relevant alternatives in the field of raw materials. This was an opportune occasion for the RHINOCEROS project to cluster with seven other EU-funded projects at the event “Production of raw materials for batteries from European sources”. The objective of the workshop was to create an environment that could foster knowledge exchange on different approaches for the recycling and recovery for battery applications. Co-organised by CROCODILE, RHINOCEROS and LICORNE, with the participation of the EU funded projects BATRAW, RESPECT, RELiEF, FREE4LIB and ENICON, the workshop gathered nearly 100 organisations driving the production and the recycling of raw materials for battery applications from primary and secondary resources.
Due to the increasing usage of batteries for electric vehicles (EVs) and energy storage systems generated by the EU’s mission to limit climate change, the demand for many metals relevant for batteries is expected to grow by more than 1000% by 2050. Held in a hybrid format, the workshop provided participants with the opportunity to discover innovation routes followed by the clustering projects on their pathway to secure sustainable and responsible sourcing of raw materials for battery production.
Nearly three hours packed with presentations provided stakeholders with essential information about each project, from the main objectives and expected outcomes, to the lessons drawn from the activities carried out.
The CROCODILE project – First of a kind commercial Compact system for the efficient Recovery of Cobalt Designed with novel Integrated Leading technologies– was presented by Dr. Lourdes Yurramendi (TECNALIA). As the most mature project, CROCODILE’s keynote focused on valuable findings and learnings regarding different aspects of the project: the samples treatment, the selection of flowsheets, the life cycle analysis (LCA) and cost (LCC) of the pilot unit, to name only a few. Later on Monday, the project was also featured as a Success Story in the Raw Materials Week, where the presentation video was played for the first time.
Download the CROCODILE presentation
Sonia Matencio Lloberas (LEITAT) presented the BATRAW project – Recycling of end-of-life battery packs for domestic raw material supply chains and enhanced circular economy. This project will develop and demonstrate two innovative pilot systems for sustainable recycling and end-of-life (EoL) management of EV batteries. Depending on the results obtained, these technologies could be extended to other types of batteries to recover all the metals and materials contained: i.e., cobalt, nickel, manganese, lithium, graphite, aluminium, and copper.
Download the BATRAW presentation
Nader Akil (PNO Innovation Belgium) explained the mission and the motivation behind the RHINOCEROS project – Batteries reuse and direct production of high performances cathodic and anodic materials and other raw materials from batteries recycling using low cost and environmentally friendly technologies. As attractive energy storage technologies, Lithium-ion batteries (LIBs) have proven to be a reliable solution, especially when it comes to the production of low-emission fleets (EVs), followed by stationary storage market and consumer electronics. According to the Strategic research Agenda for Batteries, by 2030, the global demand for LIBs is estimated to increase 14 times and the EU could account for 17%. The battery market is expected to reach 250 billion EUR/year by 2025, while the production in Europe is foreseen to rise to 300 GWh/year as of 2030. This generates opportunities for projects like RHINOCEROS to develop economically and environmentally viable routes for re-using and recycling EoL EVs and stationary energy storage Lithium-ion batteries (LIBs).
Download the RHINOCEROS presentation
Similar to the RHINOCEROS project, FREE4LIB [Feasible recovery of critical raw materials through a new circular ecosystem for a Li-ion battery cross-value chain in Europe] aims to simplify the recycling process of LIBs, as a more resilient and environmentally friendly alternative to the current linear economic model – take, make, dispose. The project, presented by Juan Castro (CARTIF), will develop six technologies at TRL5 to achieve new sustainable and efficient processes to recycle EoL LIBs: dismantling, pre-treatment and four materials recovery processes aiming to reach highly efficient materials recovery (metal oxides, metals and polymers). Additional to the recycling solutions, FREE4LIB will also target three processes dealing with metals and polymers re-using and electrode synthesis to re-manufacture new LIBs.
Download the FREE4LIB presentation
Justo Garcia (Orano Mining) presented the RESPECT project. Funded by the Horizon Europe research and innovation programme, the project aims to strengthen expertise in techniques and the value chain for the recycling of electric vehicle batteries at European level. The RESPECT project will develop a global process encompassing a process-chain flexible enough to treat all kinds of batteries in closed loop. Precisely, researchers will explore two recycling routes: full hydrometallurgy and direct recycling, and an improved Life Cycle Assessment of each recycling segment to reduce emissions, health risks and safety issues.
Download the RESPECT presentation
Recently launched, the LiCORNE project – Lithium recovery and battery-grade materials production from European resources, was introduced by Alan González Morales (PNO Innovation Belgium), who explained briefly the project’s ambitious objectives to establish the first-ever Li supply chain in Europe. With five large primary resource owners (including one of the world leaders in Li production) involved in the consortium, the project aims to increase European Li processing and refining capacity for producing battery-grade chemicals from ores, geothermal and continental brines, tailings and off specification battery cathode materials (waste).
Download the LiCORNE presentation
Gabriel Hidalgo, from the Recycling Unit of Avesta Battery & Energy Engineering (ABEE), outlined the objectives and the impact expected from the RELiEF project – Recycling of Lithium from Secondary Raw Materials and Further. Expected to boost the recycling industry, this project aims to reduce Li waste by more than 70%, and to transform recycled resources into high value battery-grade material. Relying on a very diversified consortium, RELiEF will additionally propose a new business model for materials acquisition and processing, taking into consideration environmental and social sustainability.
Download the RELiEF presentation
Sofía Riaño Torres (KU LEUVEN) presented the last EU project, ENICON– Sustainable processing of Europe’s low-grade sulphidic and lateritic nickel/cobalt ores and tailings into battery-grade metals -Launched in June 2022, the project aims to improve the refining capacity of domestic and imported low-grade Ni/Co. ENICON’s metal recovery route using hydrochloric acid dispenses with the old-school hydro-based approach that involves continuously precipitating and redissolving metals. Thus, it reduces the amount of chemicals needed for metal dissolution, which results in the production of potentially harmful waste streams. More information about the project in the joint documentary commissioned together with EU funded project NEMO: Responsible Mining in Europe.
Download the ENICON presentation
The workshop in figures
Although only in its first edition, the clustering workshop Production of raw materials for batteries from European resources attracted a diversified range of stakeholders. Counting more than 150 people registered, the audience was dominated by research organisations (26,97%), the rest of the audience being equally distributed between academia (17,76%), large companies (17,11%), SMEs (16,45%), EU institutions (4,61%) and other stakeholders addressing raw materials – national and regional administrative authorities, logistics service provides, investing companies, trade associations, NGOs, consulting companies (17,76%). Participants are located mainly in Europe but a percentage of nearly 20% shows growing enthusiasm from third countries, such as Turkey, Canada, South Korea, Chile, etc.
Exploring future clustering ideas
With the real peak of valuable outcomes from H2020 projects coming now, the aim goes beyond informing about the progress achieved to date. Building on the knowledge generated so far, new projects need to address different challenges, such as the high cost of exploration activities, the geological uncertainty, and the necessity to develop improved processing and refining technologies for better recovery of minerals and metals from side streams and industrial waste. Such challenges require close collaboration on all levels and across the entire battery value chain.
The last part of the event featured an interactive session, which included seven questions scrutinising stakeholders’ interest for similar clustering initiatives. With favourable answers and reviews, the Production of raw materials for batteries from European resources could turn into a permanent clustering hub fostering knowledge exchange and stimulating synergies between projects. More information will follow soon.
The Cluster Hub “Production of raw materials for batteries from European resources”
After the successful workshop held in November 2022, the participating projects launched in January the cluster hub carrying the same title – “Production of raw materials for batteries from European resources”. The platform is a collaboration-driven community sharing the same mission – to foster the knowledge necessary to drive a more sustainable and circular production of raw materials for the European battery industry.
Photo gallery